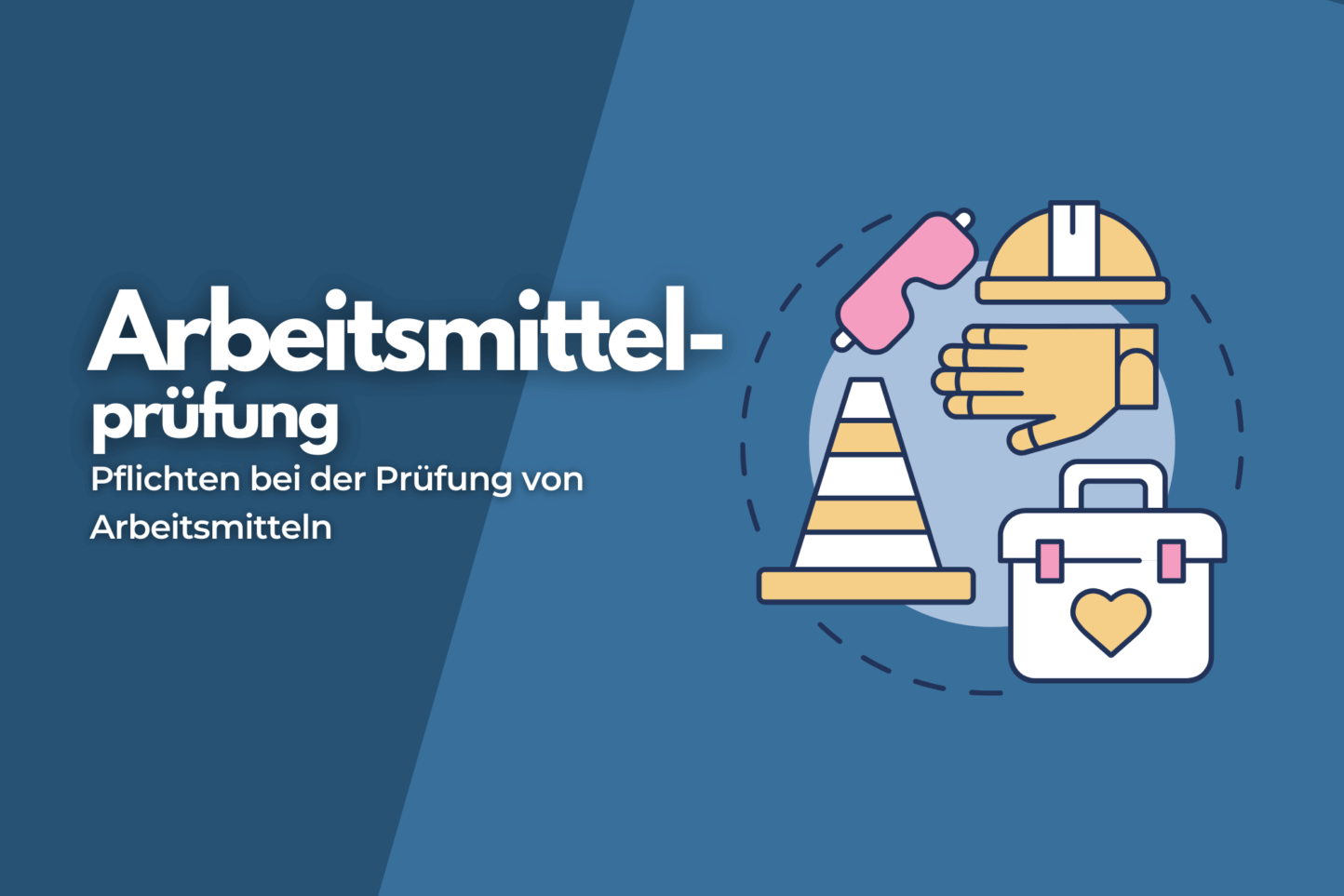
Arbeitsmittelprüfung: Pflichten, Organisation und Beispiele
- Warum sind Arbeitsmittel prüfpflichtig?
- Was umfasst Arbeitsmittelsicherheit?
- Wie hat der Gesetzgeber Arbeitsmittelprüfungen geregelt?
- Welche Pflichten gelten für Mitarbeiter hinsichtlich der Arbeitsmittelsicherheit?
- Wie organisieren Sie Ihre Arbeitsmittelprüfungen?
- Welche Angaben gehören in ein Arbeitsmittelverzeichnis?
- Beispiele zu den Prüfpflichten von Arbeitsmitteln
- Wie sind Sicherheitseinrichtungen zu prüfen?
Warum sind Arbeitsmittel prüfpflichtig?
Der Arbeitgeber steht in der Verantwortung die Sicherheit und Gesundheit im Unternehmen zu gewährleisten. So wird es vom Arbeitsschutzgesetz (ArbSchG), vom Sozialgesetzbuch VII und an anderen Stellen gefordert. Zu dieser Gesamtverantwortung des Arbeitgebers gehört auch dafür zu sorgen, dass in seinem Unternehmen nur sichere Arbeitsmittel eingesetzt und verwendet werden. Die Forderung des Arbeitsschutzes nach „sicheren Arbeitsmitteln“ klingt selbstverständlich. Doch zum tieferen Verständnis ist es hilfreich, sich diese „Sicherheit“ etwas genauer anzuschauen.
Was umfasst Arbeitsmittelsicherheit?
Arbeitsmittelsicherheit betrifft 2 Situationen:
- zum einen die Anschaffung bzw. Auswahl von Arbeitsmitteln,
- zum anderen deren dauerhafte Verwendung im Betrieb.
Anschaffung sicherer Arbeitsmittel
Unternehmen dürfen nur Arbeitsmittel beschaffen, die dem Produktsicherheitsgesetz und dessen nachgeschalteten Verordnungen (ProdSV) entsprechen. Diese, inzwischen rund ein Dutzend Verordnungen, betreffen z. B. Maschinen, Druckgeräte, elektrische Betriebsmittel, aber auch Persönliche Schutzausrüstungen (PSA). Meist erkennen Sie solche Arbeitsmittel an der CE-Kennzeichnung sowie (bei Maschinen) an der Konformitätserklärung. Darüber geben weitere Prüfsiegel und Qualitätszeichen von verschiedenen Organisationen (GS, VDE usw.) Orientierung. Damit genügt der Arbeitgeber dem ersten Teil der Pflicht, seinen Beschäftigten nur sichere Arbeitsmittel zur Verfügung zu stellen.
Sicherheit beim Verwenden der Arbeitsmittel
Der Arbeitgeber ist verpflichtet, dafür zu sorgen, dass die Sicherheit von Arbeitsmitteln dauerhaft aufrechterhalten wird. Denn diese ist bedroht durch z. B.:
- Verschleiß, Abrieb und Materialermüdung
- Verwendung außerhalb der vom Hersteller (z. B. laut Betriebsanleitung) vorgesehenen Nutzung
- Verwendung außerhalb der vorgesehenen Belastungsgrenzen
- fehlende oder mangelhafte Pflege und Wartung
- nicht fachgerechte Eigenreparaturen
Einige dieser Risiken können Ihre Mitarbeiter unmittelbar erkennen, z. B. eine abgenutzte Trennscheibe. Andere Risiken wie ein gequetschtes Elektrokabel werden allzu häufig mit einem „das geht noch“ hingenommen. Manche Risiken können jedoch nur Fachleute erkennen und bewerten, z. B. bei Elektroanlagen.
Ein Arbeitgeber kann daher nicht davon ausgehen, dass seine Beschäftigten jederzeit alle möglichen Gefährdungen durch Arbeitsmittel im Blick haben. Um die Risiken durch unsichere Arbeitsmittel aufzufangen, hat der Gesetzgeber festgelegt, dass Arbeitsmittel regelmäßig zu überprüfen sind. Art und Umfang dieser Prüfungen sowie die Anforderungen an die Prüfer sind im berufsgenossenschaftlichen und technischen Regelwerk mehr oder weniger detailliert vorgeschrieben.
Wie hat der Gesetzgeber Arbeitsmittelprüfungen geregelt?
Maßgeblich für die Sicherheit von Arbeitsmitteln ist die Betriebssicherheitsverordnung (BetrSichV) von 2015. Im Schutzkonzept der Betriebssicherheitsverordnung spielt das Prinzip des regelmäßigen Überprüfens von Arbeitsmitteln neben der Gefährdungsbeurteilung eine zentrale Rolle.
Die BetrSichV und damit die Prüfpflicht gelten für alle Arbeitsmittel, die ein Arbeitgeber seinen Beschäftigten zur Verfügung stellt. Darunter fallen Werkzeuge, Geräte, Maschinen, Anlagen und Einrichtungen. Von der Kombizange bis zur kompletten Fertigungsstraße handelt es sich um Arbeitsmittel im Sinne der BetrSichV. Regelmäßige Prüfungen sollen gewährleisten, dass der sichere Zustand eines Arbeitsmittels auch nach einer Zeit möglicherweise intensiver Beanspruchung noch besteht.
Sehen Sie diese Forderung nicht als lästige Pflicht. Mit geprüften und sicheren Arbeitsmitteln beugen Sie als Sicherheitsverantwortlicher im Unternehmen Unfällen, Verletzungen und Ausfallzeiten vor und haben Ihre Haftungsrisiken im Griff.
Bei der Frage zu den Mindestanforderungen an die Beschaffenheit von Arbeitsmitteln müsste man den Schutz vor sämtlichen Risiken nennen. Je nach Werkzeugart oder Maschinentyp sind unterschiedliche Gefährdungen betroffen, wie z. B. Quetschstellen, heiße Oberflächen, Lärm, Vibrationen, gesundheitsschädliche Emissionen, Explosionsgefahren, elektrischer Stromschlag usw.
In der Novellierung der BetrSichV von 2015 wurde das Augenmerk neben der Bereitstellung sicherer Arbeitsmittel stärker auf die Verwendung von Arbeitsmitteln zu legen. Die Prüfung von Arbeitsmitteln ist vorgeschrieben, nicht jedoch deren Instandhaltung. Das kennen Sie ähnlich von Kraftfahrzeugen. Ihr Pkw muss regelmäßig zum TÜV, diese Prüfung Ihres Fahrzeugs ist verpflichtend festgelegt: Ob Sie einen festgestellten Mangel jedoch beheben oder Ihren Wagen stilllegen und verschrotten, bleibt Ihnen überlassen. Auf keinen Fall jedoch dürfen Sie mit einem nicht verkehrstüchtigen Fahrzeug weiter unterwegs sein. Analoges gilt für Arbeitsmittel. Ob Sie einen abgebrochenen Werkzeugstiel ersetzen oder einen losen Hammerkopf befestigen lassen oder gleich ein neues Werkzeug kaufen, bleibt Ihnen überlassen. Wenn aber der Hammerkopf bei nächster Gelegenheit einen Kollegen am Kopf trifft, müssen Sie nachweisen, dass der Hammer regelmäßig geprüft und fachgerecht repariert wurde.
Zu erwarten: Besonders prüfpflichtige Arbeitsmittel
Für einige Maschinen und Anlagen sind besondere Nachweis- und Prüfpflichten vorgesehen. Welche das sind, wird im Ausschuss für Betriebssicherheit (ABS), einem Beratungsgremium des Bundesministeriums für Arbeit und Soziales (BMAS), diskutiert. Das BMAS-Forschungsvorhaben „Besonders prüfpflichtige Arbeitsmittel“ ermittelt durch eine risikobasierte Bewertungsmethode diejenigen Arbeitsmittel und Anlagen, für die eine besondere Prüfpflicht gelten soll. Diese besondere Prüfung soll durch unabhängige Experten vorgenommen werden. Die Prüfanforderungen finden Sie im Katalog der besonders prüfpflichtigen Anlagen der BetrSichV.
Welche Pflichten gelten für Mitarbeiter hinsichtlich der Arbeitsmittelsicherheit?
Die Sicherheit von Arbeitsmitteln ist keine Angelegenheit, die allein in der Verantwortung des Arbeitgebers oder auf den Schultern von Sifa und Prüfern liegt. Laut Arbeitsschutzgesetz steht jeder Beschäftigte in der Pflicht,
- zur Verfügung gestellte Arbeitsmittel nur bestimmungsgemäß zu verwenden,
- ein Arbeitsmittel vor Verwendung auf offensichtliche Mängel zu checken (Sichtprüfung),
- bei der Verwendung von Arbeitsmitteln die Bedienungsanweisung des Herstellers und die Betriebsanweisungen des Arbeitgebers zu beachten,
- die bereitgestellten Schutzvorrichtungen zu nutzen,
- ein defektes oder mangelhaftes Arbeitsmittel nicht weiter zu verwenden und unverzüglich den Vorgesetzten zu informieren,
- Reparaturen, Wartungen, Umbauten usw. nur von Personen durchführen zu lassen, die dazu vom Arbeitgeber beauftragt wurden.
Wie organisieren Sie Ihre Arbeitsmittelprüfungen?
Die Prüfung von hunderten oder tausenden Arbeitsmitteln in einem Unternehmen zu organisieren ist eine anspruchsvolle Aufgabe. Mit einem systematischen und vorausschauenden Vorgehen sorgen Sie für reibungsfreie Abläufe. Für Ihre Planung relevant sind die folgenden Aspekte.
Das Ermitteln der konkreten Prüfanforderungen kann recht aufwendig sein. Im Zweifel müssen Sie das staatliche und das berufsgenossenschaftliche Regelwerk durchgehen und nach für Ihr Arbeitsmittel relevanten Prüfvorschriften durchforsten. Lassen Sie sich ggf. von Ihrem Unfallversicherungsträger beraten, fragen Sie nach branchenbezogenen Hilfen und Prüflisten. Bei den Berufsgenossenschaften kursieren manchmal tabellarische Zusammenstellungen für prüfpflichtige Arbeitsmittel, die von Abfallsortieranlagen bis Zentrifugen unterschiedliche Beispiele mit ihren Prüfanforderungen auflisten. Doch trotz solcher Vorgaben müssen Sie immer die individuelle Situation in Ihrem Betrieb betrachten. Hilfreich, um Ihre Prüforganisation in den Griff zu bekommen, sind die folgenden 6 Fragen:
1. Was wird geprüft?
Legen Sie den Prüfumfang fest, manchmal auch als Prüfrahmen bezeichnet. Er ist abhängig von den Aufgaben und Funktionen des Arbeitsmittels und den damit verbundenen Risiken. Legen Sie fest, welche Prüfschritte vorzunehmen sind, um welche Funktionen zu testen.
2. Wann wird geprüft?
Legen Sie Prüffristen bzw. Prüfabstände fest. Vorgaben für maximale Zeitintervalle finden Sie teils in den berufsgenossenschaftlichen Vorschriften. Vorgegebene Prüffristen sollten Sie nicht pauschal übernehmen, sondern immer an die jeweiligen Bedingungen im Unternehmen anpassen. Für das Prüfintervall eines Winkelschleifers ist es z. B. ein Riesenunterschied, ob er auf einer Baustelle tagtäglich massiven Belastungen von Wetter und Baumaterialien ausgesetzt ist oder ob er in einer Feinmechaniker-Werkstatt und nur hin und wieder verwendet wird.
Unabhängig von festgelegten Fristen müssen Arbeitsmittel zum einen vor der Inbetriebnahme, nach der Beschädigung oder nach Unfällen und nach der Aufstellung an einem anderen Einsatzort geprüft werden:
3. Wie wird geprüft?
Legen Sie die Art der Prüfung fest. Gibt es vorgeschriebene Prüfmethoden? Was sagt der Hersteller, z. B. in Wartungsplänen? Was muss lediglich von außen angeschaut werden, wo müssen Arbeitsmittel geöffnet werden, wo sind z. B. bestimmte Messungen notwendig?
4. Wie intensiv wird geprüft?
Die Intensität einer Prüfung wird auch als Prüftiefe bezeichnet. Sie kann stark variieren, von einer äußeren Sichtprüfung bis zu einem Auseinandernehmen und Testen von Einzelteilen.
5. Wer darf Arbeitsmittel prüfen?
Wer was prüfen darf, geht teils aus der BetrSichV und dem nachgeschalteten technischen Regelwerk hervor. Erste Stufe ist die Prüfung durch den Benutzer selbst, z. B. in Fällen, in denen ein Mangel auch vom Laien vor der Verwendung sofort erkannt wird. In der Regel muss die Prüfung jedoch durch eine befähigte Person mit ausreichend Ausbildung, Kenntnissen und Erfahrung durchgeführt werden. Die befähigte Person muss zur Prüfung beauftragt werden. Bei höheren Gefährdungsgraden ist das Hinzuziehen eines (noch höher qualifizierten) amtlich anerkannten Sachverständigen einer zugelassenen Überwachungsstelle (ZÜS) notwendig.
Als Faustregel gilt, dass der Arbeitgeber oder eine von ihm beauftragte und unterwiesene Person in solchen Fällen prüfen darf, wenn das Arbeitsmittel
- keine überwachungsbedürftige Anlage und kein Druckgefäß darstellt,
- nicht zum Einsatz in Ex-Bereichen vorgesehen ist,
- keinen schädigenden Einflüssen (z. B. aggressiver/korrosiver Atmosphäre) unterliegt und
- seine Sicherheit nicht von den Montagebedingungen abhängt.
6. Was wird wie dokumentiert?
Eine Plakette oder ein Prüfzeichen anzubringen ist noch kein Nachweis einer Prüfung und als alleinige Dokumentation etwas dürftig. Wenn eine Behörde oder Ihr Unfallversicherungsträger Ihre gesetzlich vorgeschriebene Prüffristen-Dokumentation sehen will, sollten Sie schriftliche Aufzeichnungen vorlegen können.
Die Form der Prüfaufzeichnungen und ihrer Verwaltung ist Ihnen freigestellt. Sie können Prüfberichte abheften, Prüfbücher führen, ein Karteikartensystem anlegen oder Ihre Prüfungen am PC verwalten. Wichtig ist, dass aus diesen Unterlagen Art und Umfang der Prüfung, Prüfergebnis, Prüfdatum und Prüfer ersichtlich werden. Es gibt inzwischen raffinierte Software-Lösungen für Prüffristenverwaltung und Prüffristenmanagement.
Achten Sie darauf, dass Ihre prüfenden Mitarbeiter nicht in den häufigen Fehler verfallen, bei einem „nix gefunden“ das Blatt leer zu lassen und nur die expliziten Fehler und Mängel zu notieren. Ist mit einem Arbeitsmittel alles in bester Ordnung, ist selbstverständlich z. B. „keine erkennbaren Mängel“ zu notieren. Ansonsten könnten Sie später nicht nachweisen, dass geprüft wurde.
Welche Angaben gehören in ein Arbeitsmittelverzeichnis?
Sie behalten den Überblick und erleichtern sich auf Dauer Ihre Arbeit, wenn Sie alle Geräte, Maschinen, Anlagen usw. systematisch erfassen und katalogisieren. Mit einem solchen klug angelegten und sorgfältig geführten Arbeitsmittel- oder Anlagenkataster können Sie im Ernstfall nachweisen, dass Sie Ihren Prüfpflichten nachgekommen sind und mögliche Gefahren und Gefährdungen rechtzeitig entschärft haben. Folgende Angaben gehören in ein Arbeitsmittelverzeichnis:
- Name oder Bezeichnung des Arbeitsmittels
- die festgelegte Prüffrist (ggf. mit Begründung der Prüffrist)
- die Angabe der befähigten Person (z. B. den Kundendienst des Herstellers)
- die Art der Dokumentation der Prüfung (z. B. Prüfbuch, Prüfliste, Prüfplakette)
- die Beschreibung des Prüfumfangs bzw. ein Verweis darauf (z. B. eine Wartungsanleitung des Herstellers)
Anhand dieser Übersicht können Sie gleichartige Arbeitsmittel zu einer Arbeitsmittelgruppe zusammenfassen und ggf. Prüfumfang, Prüffristen usw. gemeinsam festlegen, z. B. für alle Elektro-Gabelstapler.
So nutzen Sie die TRBS 1201
Konkretere Vorgaben zur Prüfung von Arbeitsmitteln liefert die Technische Regel für Betriebssicherheit (TRBS) 1201 „Prüfung von Arbeitsmitteln und überwachungsbedürftigen Anlagen“. Sie gilt übrigens auch für nicht überwachungsbedürftige Arbeitsmittel. Die TRBS 1201 unterscheidet Prüfungen nach
§ 3 Abs. 3 BetrSichV: Das sind die „Routine“-Prüfungen auf Basis der Gefährdungsbeurteilung.
Prüfungen nach § 10 BetrSichV: Dies betrifft besondere Fälle wie die Prüfung nach Montage vor erster Inbetriebnahme und Prüfungen nach Beschädigungen, Reparaturen, Unfällen und anderen außergewöhnlichen Ereignissen. Diese Prüfungen sind von einer befähigten Person vorzunehmen.
Prüfungen nach Anhang 4 Abschnitt A Nr. 3.8 BetrSichV: Dies betrifft Arbeitsmittel in explosionsgefährdeten Bereichen. Hier dürfen Prüfungen nur durch befähigte Personen vorgenommen werden, die über besondere Kenntnisse im Ex-Schutz verfügen.
Prüfungen an überwachungsbedürftigen Anlagen nach den §§ 14, 15 und 17 BetrSichV: Darunter fallen z. B. Druckgeräte, Pressen und Röhrenöfen. Prüfungen sind nur durch zugelassene Überwachungsstellen oder befähigte Personen möglich.
Mit den diversen Prüfzeichen unabhängiger Organisationen und Prüfstellen wie VDE-Zeichen oder GS-Zeichen haben Sie als Fachkraft für Arbeitssicherheit in der Regel nicht aktiv zu tun.
Beispiele zu den Prüfpflichten von Arbeitsmitteln
Für viele prüfpflichtige Einrichtungen macht das berufsgenossenschaftliche Regelwerk Vorgaben zu Frequenz, Art und Umfang der Prüfungen. Dies ist z. B. für elektrische Anlagen und Betriebsmittel der Fall sowie für Flurförderfahrzeuge, Hebezeuge, Lastaufnahmeeinrichtungen, Hebebühnen, Pressen, Ketten, Leitern u. a.
Nachfolgend ergänzende Anmerkungen zu einigen häufig nachgefragten Prüfsituationen:
Regale und Lagersysteme
Nicht nur die BetrSichV schreibt regelmäßige Prüfungen vor. Für einige Arbeitsmittel kommen normative Regelungen hinzu. So fordert z. B. die europäische Norm DIN EN 15635 von 2009 vom Betreiber eines Lagers, dass er die Regaleinrichtungen regelmäßig durch eine fachkundige Person inspizieren lässt.
In Betrieben mit umfangreicher Lagerhaltung oder wenn Sie Regalsysteme unterschiedlicher Hersteller nutzen, ist es oft sinnvoll, einen eigenen Mitarbeiter zur „Befähigten Person zur Prüfung von Regalsystemen“ qualifizieren zu lassen. Dann sparen Sie mittelfristig Kosten und müssen nicht externe Prüfer anfordern.
Leitern und Tritte
Auch und gerade solche „banalen“ Arbeitsmittel wie Leitern müssen regelmäßig auf ihren ordnungsgemäßen Zustand geprüft werden. Bei einer Vielzahl von Leitern im Unternehmen kann es hilfreich sein, alle Leitern durchzunummerieren. Auch ein spezielles Prüfbuch für Leitern (Leiternkontrollbuch) ist dann zu empfehlen.
Gabelstapler
Gabelstapler sind ein schönes Beispiel dafür, dass die Prüfvorgaben nicht einfach übernommen werden sollten. Normalerweise ist mindestens einmal im Jahr eine Prüfung vorgesehen. Je nach Einsatz Ihrer Stapler kann das aber häufiger oder weniger häufig nötig sein. Ein Stapler, den Sie nur selten nutzen, brauchen Sie meist auch nur seltener zu prüfen. Bei einer hohen Jahreskilometerleistung kann das Jahresintervall dagegen zu lang sein. Denn für die Ermittlung der Prüffrist eines Gabelstaplers ist es ein Riesenunterschied, ob er z. B. nur hin und wieder zum Transport eines schweren Gegenstands benötigt wird oder ob er im 3-Schicht-Betrieb im Dauereinsatz ist. Auch hier empfiehlt sich das Führen eines Prüfbuches, welches die Flurförderfahrzeuge identifiziert und Ihre Prüfvorgänge dokumentiert.
Elektrische Anlagen und Betriebsmittel
Die Anforderungen an die Prüfung elektrischer Anlagen und elektrischer Betriebsmittel sind ein Kapitel für sich und ein komplexes dazu. Man unterscheidet ortsfeste und nicht ortsfeste elektrische Betriebsmittel. Für Letztere gelten in der Regel kürzere Prüffristen. Für die Fachkraft für Arbeitssicherheit ist wichtig zu wissen, dass alle Elektro-Prüfungen zu erfolgen haben und nur durch eine Elektrofachkraft oder unter Aufsicht einer Elektrofachkraft, vor der ersten Inbetriebnahme, und dann in regelmäßigen Zeitabständen sowie
- nach Änderungen, Reparaturen und Wiederinbetriebnahmen. Oft wird die Frage gestellt, inwiefern eine elektrotechnisch unterwiesene Person (euP) solche Elektroprüfungen vornehmen darf. Dies ist nicht per se verboten, aber nur erlaubt
- in einem begrenzten Umfang, z. B. wenn es nur darum geht, an einem ortsveränderlichen Betriebsmittel mit einem entsprechenden Messgerät die Spannungsfreiheit festzustellen,
- unter Aufsicht und Leitung einer Elektrofachkraft.
Feuerlöscher
Handfeuerlöscher in Arbeitsstätten müssen alle 2 Jahre und nach jeder Benutzung durch eine befähigte Person geprüft werden. Nach erfolgreicher Prüfung erhält der Feuerlöscher eine Plakette. Aus dieser geht auch das Datum der nächsten Prüfung hervor.
Anschlagmittel
Bei Anschlagmitteln wie Ketten, Seilen, Rundschlingen usw. ist unmittelbar einzusehen, dass der sie benutzende Mitarbeiter sie vor jeder Verwendung in Augenschein nehmen sollte. Jeder Mangel und jede Beschädigung können lebensgefährlich werden. Darüber hinaus sind alle Anschlagmittel und Lastaufnahmemittel mindestens einmal jährlich durch eine befähigte Person zu prüfen.
Wie sind Sicherheitseinrichtungen zu prüfen?
Haben Sie als Fachkraft für Arbeitssicherheit den Überblick über alle technischen Sicherheitseinrichtungen in Ihrem Betrieb? Auch Notausschalter, Laborabzüge, Gaswarngeräte, Augenduschen usw. müssen laut Arbeitsstättenverordnung regelmäßig überprüft werden, um zu gewährleisten, dass sie im Notfall auch einwandfrei funktionieren.
Vergessen Sie nicht die Organisation der Prüfungen aller Einrichtungen zur Flucht und Rettung. Gerade weil man hofft, sie niemals verwenden zu müssen, sollten hier alle Mechanismen funktionieren. Das betrifft z. B. Verriegelungssysteme von Notausgängen oder Systeme zur Sicherheitsbeleuchtung bei Stromausfall.
Prüfverfahren auf dem Prüfstand
Zwar sollten Prüfprozedere festgelegt sein, aber das bedeutet nicht, dass sie etwas Statisches wären. Der Stand der Technik entwickelt sich weiter und neue Technologien und Materialien verbessern immer wieder die Prüf- und Messmethoden.
Es lohnt sich daher, auch bewährte Prüfverfahren hin und wieder auf den Prüfstand zu stellen oder sich z. B. auf Fachmessen über die aktuelle Prüf- und Messtechnik zu informieren. Oft sind neue Messgeräte und -systeme nicht nur leistungsfähiger, sondern auch aus Arbeitsschützer-Sicht wünschenswert.